Developing a new type of aircraft is always fraught with challenges. But when that aircraft is intended to fly in the stratosphere for months at a time, it’s a whole different set of problems.
For companies working to bring high-altitude platform stations (HAPS) into service, there is no well-trod pathway. Touted as an elegant solution to high-resolution surveillance, communications, and environmental monitoring in difficult-to-reach parts of the world, HAPS has been recognized by the World Economic Forum as a critical emerging technology.
But testing a HAPS aircraft is nothing like testing a conventional aircraft or even a satellite. These aircraft face extreme environmental conditions, low air density and a completely different aerodynamic regimen in a part of the atmosphere that is less understood.
Despite the immensity of the challenges HAPS present, the opportunities are great and so a handful of companies are striving to develop a solution. While technical and regulatory issues still need to be overcome, advances in solar power, AI-driven flight management, and lightweight materials are pushing HAPS closer to large-scale deployment.
Ground testing
Naturally, any HAPS vehicle will undergo the usual simulation, architecture and modeling well before production. Once the design is locked in, engineers must ensure every part of the aircraft and its components can withstand stratospheric operations.
Thermal vacuum chambers are needed to replicate the extreme conditions HAPS will experience. Widely used in the space industry, these chambers allow an aircraft’s components to be tested in environments that are equivalent to those in the stratosphere.
“It’s an essential bit of kit for what we do,” says Graham Holland, chief technical officer at Prismatic, a subsidiary of BAE Systems, which is developing the PHASA-35 HAPS. “We can’t just go to a normal test house, because the standard aerospace test chambers don’t go as cold and as high in altitude as we need.”
“We can either run sections of the aircraft or entire subsystems inside there,” explains Ed Townshend, flight test lead engineer for PHASA-35. “We can do long-duration tests of the components, and also cycle the pressure and temperature variations to replicate fully the sort of environment it’s going to be subjected to.”
Some pre-flight testing is more familiar, such as stress tesing, which has seen more than one broken wing in conventional aircraft. For HAPS, with zero rivets and a bonded construction, testing its integrity is essential.
“Every airframe is tested and loaded up to more than 2g to validate the quality, especially of the bonding,” explains Pierre-Antoine Aubourg, chief technical officer at Aalto, the Airbus subsidiary that oversees Zephyr HAPS.
“We will do this until we are fully convinced of the maturity of the supply chain.”
But have any wings been broken? “Yes,” says Holland. “When you’re trying to push the limits of what is possible, you need to understand the materials you are working with.
“We do ultimate load testing and then go even further to understand the failure mechanisms because that’s hugely important as part of that understanding.”
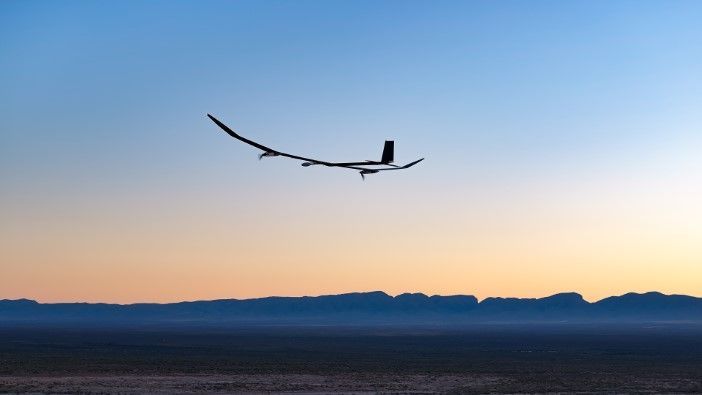
(Photo: BAE Systems)
Weather watchers
Before a HAPS can leave the ground, the conditions need to be right. Wind speeds of more than 20 to 30 knots or low cloud can prevent a launch. This means having knowing the meteorological conditions at the launch site and along the flight path.
“We set up a dedicated team looking at weather forecasting to interpret all the data according to our specific need,” says Aubourg. “We look at everything from launch location to global weather patterns to ensure we have access to the stratosphere without risk.”
The Prismatic team works with the Met Office in the UK for weather reporting and has a professional meteorology team on hand for interpretation. In addition, they use Honeywell’s High Altitude LiDAR Atmospheric Sensing (HALAS), combining data from this and other weather models to get the most accurate prediction of conditions.
Needing to be very efficient on the climb, PHASA-35’s first stratospheric flight in 2023 was undertaken with low airspeed. This meant it was more susceptible to the wind, and it was pushed back substantially during the flight. “In that first flight trial, we were flying backward for around 70km,” notes Holland.
But thanks to extensive weather data, it wasn’t a surprise and had been planned for before the aircraft left the ground. “We had been validating the models such that we can predict performance, the meteorology, the location, the drift back,” explains Townshend. “We knew exactly how far we were going to drift back and we had a very good prediction of what was going to happen.”
Flight testing
Being some of the first to extensively explore the stratosphere means HAPS companies are collecting large quantities of data on the environment. With more than 5,000 flight hours in the upper atmosphere, Aalto has begun to make some interesting discoveries.
“We can characterize gravity waves in the stratosphere and use them like a surfer,” says Aubourg. “It means we can optimize our trajectory and our transit in the stratosphere.”
While deep knowledge of the upper atmosphere is still a work in progress, survival at these extreme altitudes is not such an issue. “It’s very benign in the stratosphere, the winds are very low,” says Holland. “The transit is the most difficult bit. We see it as the highest risk portion of any of our flights.”
By their nature, HAPS are very lightweight aircraft. The Zephyr has a maximum takeoff weight (MTOW) of around 75kg (165 lbs), with 5kg (11 lbs) of payload. The PHASA-35 is heavier at 150kg (330 lbs) MTOW, but with 15kg (33 lbs) of payload.
Both are primarily made from carbon-fiber composite with most of the weight coming from the lithium-ion batteries, putting the aircraft at risk of buffeting and structural damage in the troposphere.
“Our biggest challenge to entering into mass operation is to ensure survivability during access to the stratosphere and recovery,” explains Aubourg. “We had several learning experiences in the past, where we encountered some early termination of aircraft due to thermal activity and turbulence.”
In response to this, Aalto undertook a complete redesign of Zephyr’s flight control laws, tailoring to the elasticity of the aircraft and giving more control during turbulence. Testing in 2023 over half a day proved the new configuration, with Zephyr successfully controlled at very low altitudes of around 6,000 ft.
“As a result, we were able to significantly extend the flight domain and survive in situations where in the past, we could have lost the aircraft,” explains Aubourg.
Test flights are a great opportunity to understand HAPS better, and the Aalto Zephyr’s latest flights have been fully instrumented with accelerometers, pressure sensors and other equipment. “It helps us understand load distribution on the aircraft, the behavior, and allows us to validate our models,” says Aubourg.
“The wonderful thing about HAPS aircraft is that your missions are substantially longer than test flights with commercial aircraft,” notes Holland. “We can do a huge amount of data collection because we’re up for so long.”
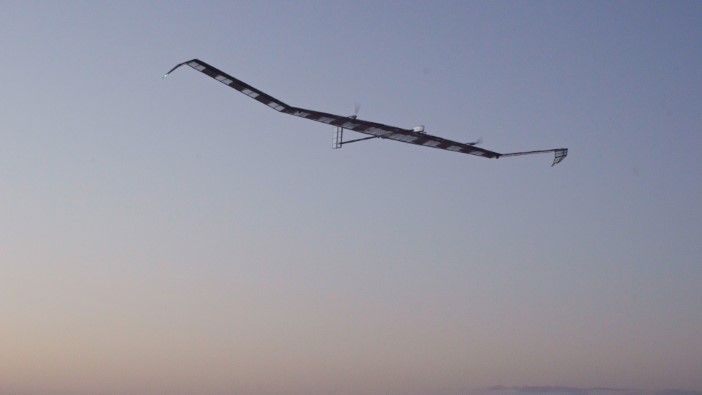
Operational readiness
In early 2025, Aalto took Zephyr on a milestone 13-day flight equipped with direct-to-device (D2D) 4/5G connectivity payload, developed in-house at its Farnborough facility. As well as testing this technology, the flight validated its improvements to the flight envelope and put new power conservation strategies through their paces.
But the most remarkable element of Zephyr’s first 2025 flight was where it was launched from. For the first time, Zephyr took off not from Arizona, but from Laikipia County in Kenya, from the company’s own ‘Aaltoport’, the world’s first purpose-built HAPS facility.
“Being able to launch from our base in a place that can offer seven to eight months access to the stratosphere is a significant step forward,” says Aubourg.
“Over the last year, we increased the maturity of the aircraft and its ability to survive adverse conditions, and now we will have more launch opportunities. Altogether, we are making great progress on our readiness to start commercial operations.”
For Prismatic, the PHASA-35 is reaching a key transitional phase towards operational readiness. Under test in recent flights has been its Block 10 aircraft with a limited solar array. Coming in 2025 will be Block 20, covered top to tail in solar panels and equipped with next-gen power systems. The new model has more than twice the onboard solar power generation and storage capacity than the current version.
“We know we can fly in the stratosphere. We know it works as we intend it to, and now we want to be able to do that as a sustained flight,” explains Holland. “That’s the target for this year, is to prove out that next-gen system on multi-day flights.”
With no defined route to certification of these aircraft, companies like Aalto and Prismatic must obtain permission for every take-off. Being able to certify HAPS would remove this barrier and make flights much easier to schedule. “We will not have commercial operation without certification,” says Aubourg. “We’re working with the UK CAA to define a certification pathway, and hope to conclude this by next year. That will simplify our life.”
“There is no certification base we can pick up on, but we need to get there,” notes Holland.
“There’s lots of work ongoing with regulators and the industry trying to figure out the route forward. Do we need a formal type certificate? I don’t think we have an answer to that yet.”
Following the 13-day Kenya debut, Aalto’s next campaign plans to push endurance limits even further. Ultimately, the company has set its sights on fully autonomous continuous operation for over 100 days. This would be a record, already held by Zephyr with a 64-day flight in 2022. But Aalto insists they are not just chasing accolades, as future flights will focus on demonstrating the full end-to-end capability for future customers.
Everything these groundbreaking aircraft have achieved to date has been done with existing battery technology. As that technology evolves, HAPS could ultimately be even more capable.
“Any saving on the weight of the battery can be used for something else: to fly longer, higher altitude or with bigger payloads,” says Aubourg. “We are pushing our supplier to improve all the time.”