Parachutes are essential in decelerating spacecraft, delivering airdropped payloads, aiding pilot ejections, and more. Traditional methods of assessing parachute performance measure permeability and tensile strength, but recent advances in computing enable more sophisticated modeling and simulation of parachute dynamics. Modeling can reduce the cost, labor, and time needed to create mission specific textiles, by connecting fabric porosity, microstructure, and canopy mechanics to overall performance. But, the models require high-fidelity experimental data for accurate validation.
In our study, we subjected military-standard parachute textiles to radial in-plane loads in a step-wise load-to-failure pattern using a bespoke tensile testing apparatus and used micro-CT (computed tomography) imaging to examine how microstructural variations impact tensile response.
A high-precision linear actuator with 4µm steps controlled displacement and could withstand up to 120lbf.
The use of x-ray micro-CT to capture sub-micrometer details and semi-automated tools to extract data about the textile’s architecture from 3D images enables a faster way to produce the data and characterize these materials.
Fabric samples were cut into 55.9mm-diameter circular coupons and imaged with a 3.7mm field of view (FOV) positioned to exclude large ripstop tows, allowing focus on the bulk weave structure. Imaging at 1.9 µm/pixel resolution with a 4× lens provided high-detail data for targeted analysis.
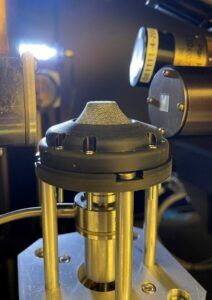
For image analysis, we employed a 3D U-NET segmentation technique, a method proven effective for low-contrast imaging in medical fields, to differentiate warp and weft tows – the perpendicular weave axes, in the images. Using an in-house framework, we semi-automatically extracted critical metrics such as dimensions, crimp angles, spacing between tows and pore sizes and assessed them relative to the radial stress applied.
Our findings show that the anisotropic response of parachute textiles under planar loads is strongly influenced by manufacturing methods, pretension, and the composition of warp and weft tows in terms of fiber count and size. Even with homogenous tow composition, manufacturing-induced pretension caused anisotropic behavior, with warp pretension accelerating weft decrimping under load. This resulted in weft-axis strains approximately 10% to 20% larger than those along the warp axis.
Understanding this difference can inform processes like parachute assembly. Parachutes are made of different textile pieces that are attached to each other, and the orientation of these pieces influences the properties of the overall parachute. Choosing the best parachute materials is crucial for safety and mission goals. This research can inform models that will be used to identify promising candidate textiles.
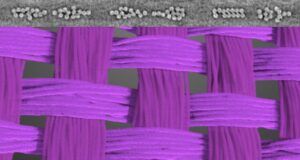
Improving models for screening parachute materials makes parachute manufacturing and applications more cost effective and time efficient. In addition to scientific missions, this work can be applied to parachutes in other settings: for instance, use in relief efforts or in recreation.
The study was published in the American Institute of Aeronautics and Astronautics Journal in August 2024. The next stage of the research is using microscopy imaging to better understand how textile pores impact airflow, as well as imaging textiles with flow passing through them to visualize the 3D deformation.