Researchers from the USA have found stacked co-rotating rotors offer a way to develop electric vertical takeoff and landing aircraft capable of hovering silently.
Researchers from the US Army Combat Capabilities Development Command – DEVCOM Army Research Laboratory, Uber and the University of Texas at Austin have been examining the acoustic properties of the rotors used by electric vertical takeoff and landing (eVTOL) aircraft as part of a two-year study. This has included testing and modelling technologies such as co-rotating rotors.
The results of the research program, Experimental and Computational Investigation of Stacked Rotor Acoustics in Hove, have been published in the Vertical Flight Society 76th Annual Forum Proceedings.
The US Army wants to use eVTOLs for aerial surveillance and cargo transport. However eVTOLs, which have smaller rotors than helicopters that are electrically-powered, emit a different sound signature that is largely unaccounted for in current simulation models and knowledge.
George Jacobellis, US Army research engineer at the US Army Research laboratory’s Vehicle Technology Directorate said, “The noise you hear from these smaller rotors is generated through different physical mechanisms.
“Traditional modeling techniques need to be improved to account for all of the noise generated so that vehicle designers can be aware of what will actually be heard.”
Thickness noise
Standard helicopter noise simulations focus primarily on predicting thickness noise and loading noise, because they constitute the dominant noise sources for large helicopters.
Thickness noise stems from the displacement of the air by the rotor blades, while loading noise occurs when lift and drag forces act on the air that flows around the rotary wings. Together, they make up what experts refer to as tonal noise.
In contrast, Army researchers suspected that eVTOL rotors generate more broadband noise, which refers to sounds caused by turbulence, than tonal noise.
“We didn’t know whether broadband noise was important or not, but we knew that the tonal and broadband noise scaled differently,” Jacobellis said. “We thought that as rotors became smaller there would be some point at which broadband noise would be the dominant source.”
Test setup
The team confirmed their hypothesis in their research study, which measured the acoustic characteristics of various eVTOL rotor configurations but also assessed the modeling capabilities of helicopter noise simulations for eVTOL rotors.
During the field experiment, the researchers set up a test stand with two electrically-powered rotors and recorded the noise generated above and below the rotor plane with nine microphones placed in a circular array surrounding the rotor hub.
Two- and four-bladed rotors with a 1.1m radius in hover were measured experimentally at rotor speeds up to 1200 RPM and tip Mach number up to 0.41.
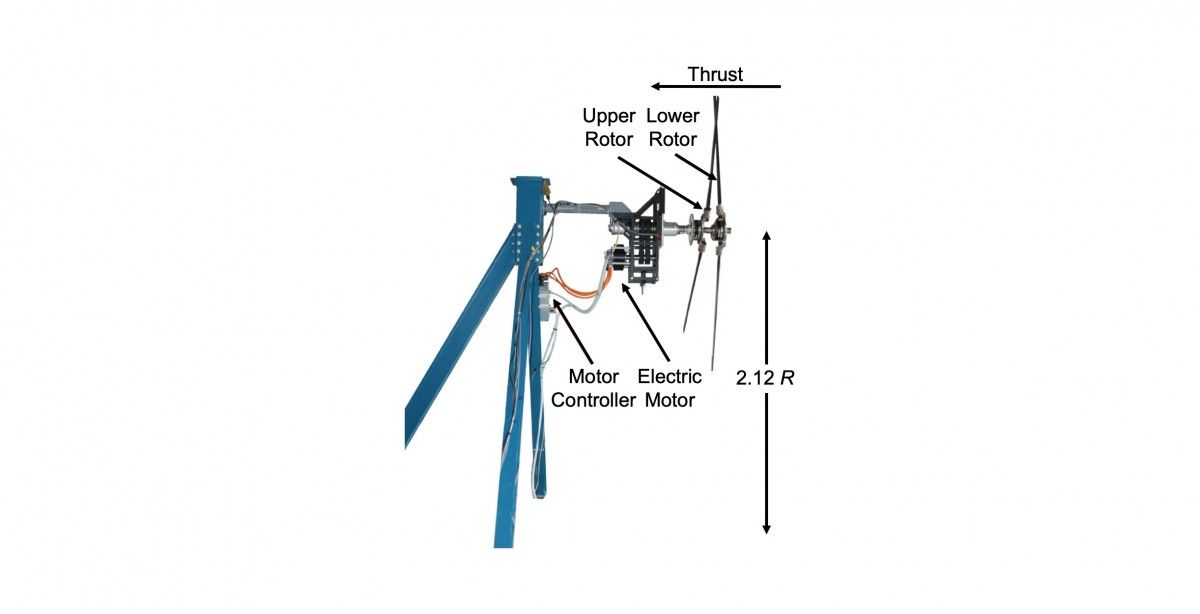
For the simulations, the team used the Rotorcraft Comprehensive Analysis System (RCAS) and a routine noise prediction code called PSU-WOPWOP, named onomatopoeically for the sound that helicopter blades make.
Jacobellis said, “RCAS computes the aerodynamic loads, or forces, on the blades as well as the bending and twisting of the blades.
“This information is necessary to use as inputs to PSU-WOPWOP, which computes the noise generated by the rotor. Connecting the two programs required a significant amount of work, which was done by our group as well.”
The researchers modeled the broadband noise in PSU-WOPWOP with Pegg’s method, one of the two settings present in the simulation program with the other called Brooks’ method.
While Pegg’s method makes broadband noise predictions based off of experimental data of the entire rotor, Brooks’ method accounts for the unique distribution of lift along the blade.
“These technologies are promising in their ability to predict the noise of eVTOL rotors, but we need to do more work to obtain acceptable accuracy,” Jacobellis said. “The next steps are to implement the Brooks method for higher accuracy acoustic predictions and to compare the unsteady loads between the simulation and experiment to check the accuracy of the simulations in predicting the unsteady loads.
“The Brooks method should be better at capturing unique configurations and loading distributions.”
Stacked rotors
Researchers also found that co-axial co-rotating rotors, or stacked rotors, may offer better performance and lower noise than a conventional rotor. Unlike conventional rotors which employ blades arranged in a single plane, stacked rotors place blades in multiple planes.
According to the results of their study, stacked rotors with equally spaced rotor blades produced the lowest noise level, around the same level as that of a traditional rotor.
By investigating different values of axial spacing, Army researchers believe that they may uncover a stacked rotor configuration that produces lower noise than the conventional rotor.
“I do think that a stacked rotor can be beneficial for eVTOL applications,” Jacobellis said. “The added degree of freedom for the design will allow for gains in efficiency and control over the acoustic signature, which has been shown in the results. More investigation is needed to quantify the noise reduction with axial spacing.”
This article was originally posted by the US Army website and has been edited for style and length.